A combined compressor house (CCH) control system replacement project, undertaken by NJCSI (Pty) Ltd. (NJC), an ABB Authorised Value Provider (AVP), has won high praise from the client ArcelorMittal. “The professionalism, dedication, and attention to detail have exceeded our expectations,” says Erich Blaschczok, Senior Electrical Engineer, Information Management, at ArcelorMittal.
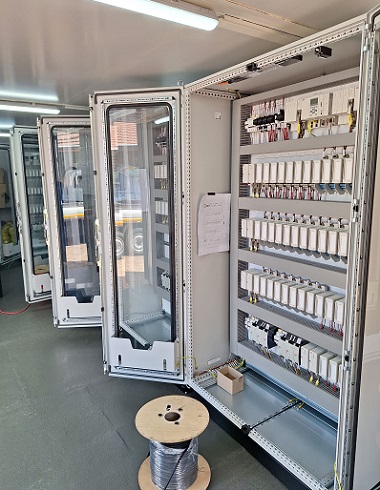
The project was critical as the combined compressor house supplies all instrumentation air, blast air for the blast furnaces, and other air requirements for the Vanderbijlpark facility. Thia also meant that it was not practical to initiate a major shutdown, as the CCH is integral to the entire operation. NJC CEO, Sarane Richard-Coombes notes: “The project required meticulous planning, clear communication, and unwavering support.”
Sebastian Lopes Pereira, DCS Engineer at NJC highlights, for instance, that the rewiring of panels involved 12 000 I/O points.
ArcelorMittal entrusted the production-critical project to NJC as they have a longstanding business relationship, ongoing now for over a decade. “What gave us the edge in securing this project is that competitors insisted on a shutdown, which was a non-negotiable for the client,” Pereira adds.
With this project, the latest of three projects it has carried out at ArcelorMittal over the years, NJC continued to develop its reference record of successful project implementation. The six-month project was completed and handed over in December 2024.
Sagren Govender, Business Development Manager at NJC, adds that the support received from ABB was exceptional, with stock of key components available at all times, as well as expert assistance and support.
NJC has been an AVP for ABB Control Technologies since 2016. The companies had worked on their first joint project in 2006. Since then, NJC has completed many projects using ABB systems across southern Africa. It is skilled in the ABB Ability™ System 800xA and Manufacturing Execution Systems (MES) for various industry sectors, from food and beverages to pharmaceuticals, pulp and paper, and mining and metals.
Kristian Olsson, Global Head of Partner and OEM Sales, ABB Control Technologies, says, “NJC is a valuable partner for us in the southern Africa region. The company is a great example of a best-in-class system integrator that is well positioned in several key growth sectors on the continent.”
NJC is a professional engineering service provider of process control, automation, and information systems. It designs and installs control systems and management systems that meet customers‘ specifications for performance and reliability. It has established a name for itself in the local automation industry since its inception in 1997.
“Global leaders such as ABB have selected us as their channel partner for the design and implementation of their products and systems. Based on a solid engineering background and with a diverse resource base of experienced professionals, we provide a complete service to industrial and corporate companies.
“Our mission is to deliver excellence in industrial IT and control systems to facilitate world-class production environments. We aim to be a provider of choice based on our reputation for delivering quality, innovative solutions that represent outstanding value for our clients,” says Richard-Coombes.
NJC’s engineering services enable clients to optimise their production processes and to form a clear picture of how to manage them. Its experienced automation specialists cover all areas within automation engineering and industrial IT, including management information systems, S88 compliant batch system integration, process control and optimisation, electrical and instrumentation engineering, turnkey industrial automation projects, PLC/SCADA systems, distributed control systems, advanced batch handling and MES integration solutions, automation engineering consulting, and safety systems compliance.
ABB’s control technologies, particularly ABB Ability™ System 800xA and MES, offer significant advantages for the metals industry in enhancing productivity, quality, and sustainability. They go beyond traditional distributed control systems, integrating process control, electrical control, safety systems, and asset management into a unified platform.
This integration provides for real-time monitoring and optimisation of metallurgical processes such as in steelmaking and rolling mills. Maintaining precise control over operations, it helps reduce defects, ensuring consistency in metal properties. At the same time, it optimises energy consumption in energy-intensive processes like electric arc furnaces and reheating furnaces. Through its compatibility with existing systems, including ERP and third-party solutions, ABB Ability™ System 800xA provides complete operational visibility, leading to more efficient decision-making and higher overall efficiency.
MES, the manufacturing execution system, complements this by bridging the gap between business planning and plant operations. With real-time production tracking, MES solutions monitor work in progress, yield, and quality deviations, helping to optimise output and minimise material waste. They also improve inventory management by ensuring the efficient use of raw materials, reducing costs and preventing production slowdowns.
Predictive maintenance capabilities further enhance uptime by identifying potential equipment failures before they occur, to support continuous and reliable operations. Additionally, MES solutions support regulatory compliance by automating the tracking of emissions, energy usage, and production parameters, making it easier for companies to meet environmental and industry standards.
For more information visit: www.go.abb/processautomation