South Africa’s solar energy sector is seeing unprecedented growth. The South African Photovoltaic Industry Association (SAPVIA) reports over 6 200 MW of rooftop solar installed by early 2025, a 15% increase over the previous year.
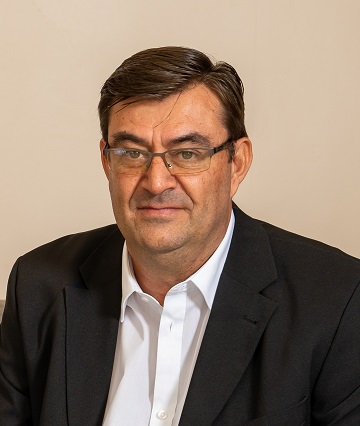
While this increase reflects the need for secure energy supply and the nation’s commitment to a sustainable energy future, Tertius Ness, Chief Operating Officer at South Ocean Electric Wire (SOEW), highlights that it also exposes a critical vulnerability: the widespread use of poor-quality solar cables. He says reports indicate that one in six fires attended to by South African firefighting services is linked to substandard solar installations, often due to faulty wiring or incompatible components.
High-profile incidents, such as the 2023 fire at a communications company’s Cape Town headquarters, suspected to be caused by solar panel wiring, and a 2024 warehouse explosion in Durban, where arcing from substandard solar cables ignited flammable materials, have resulted in millions of rand in damages. These events underscore the severe risks of electrical faults, overheating, short circuits and explosions, which can lead to property damage, injuries and in some cases, fatalities, threatening public safety and the credibility of solar energy adoption.
Ness says the rapid expansion of solar installations has led to an influx of cheap, substandard cables, many of which are imported and do not meet international standards like BS EN 50618 and IEC 62930, the latter adopted by the South African Bureau of Standards (SABS) as SANS/IEC 62930. These standards are designed to ensure that solar cables can withstand the harsh African climate with its extreme temperatures, UV radiation and humidity.
“However, irresponsible manufacturers often cut corners, using inferior materials that degrade quickly under environmental stress. Such cables are prone to insulation breakdown, which can lead to arcing, overheating and fire hazards,“ says Ness. “The 2024 explosion at the warehouse in Durban, for instance, was traced back to a substandard cable that could not handle the electrical load, resulting in a catastrophic failure that ignited nearby materials.”
He adds that, beyond safety, such substandard cables reduce the efficiency of photovoltaic (PV) systems, lowering energy output and compromising the financial viability of solar projects.
Solar cables are critical in PV systems, transmitting power from panels to inverters and further. Their performance hinges on rigorous manufacturing and testing standards. Key tests outlined in international standards include thermal endurance to assess heat resistance, UV and weathering tests to ensure durability against environmental factors, and ozone resistance to prevent insulation degradation.
Other tests include damp-heat testing to evaluate performance in humid conditions, dynamic penetration tests to measure mechanical resilience, voltage tests to confirm insulation integrity, and hot-set tests to verify the degree of cross-linking for thermal and mechanical stability.
Ness says cables that bypass these tests, often sold as “solar cables” but made with standard PVC insulation, do not have the necessary durability and will have a lifespan much shorter than the 15 years expected of high-quality solar cables. As well as jeopardising safety, this undermines the long-term reliability of solar installations, potentially deterring future investment in renewable energy.
The use of substandard cables also raises economic concerns resulting from decreased conversion efficiency which reduces a plant’s ability to generate planned production outputs. For large-scale projects, this can translate into significant financial losses, and for smaller-scale installations, it means higher electricity costs due to system inefficiencies.
Furthermore, the costs of replacing failed cables and repairing damage from fires or electrical faults far outweigh the initial savings of opting for cheaper products. Ness acknowledges that in a price-sensitive market like South Africa, the temptation to choose lower-cost options is understandable, but the adage ‘you get what you pay for’ rings true. He cautions that cables at significantly below market average prices are often made with substandard materials, unable to withstand the mechanical and environmental stresses of solar applications.
To mitigate these risks, buyers should prioritise cables that adhere to local and international standards, ensuring they have undergone comprehensive testing for safety and performance. They should look for manufacturers with a proven track record of quality and compliance, offering transparency on their testing regimes and material specifications.
High-conductivity tinned copper conductors and cross-linked polyolefin (XLPO) insulation are hallmarks of durable solar cables, capable of withstanding the African climate. Additionally, choosing locally manufactured products can support South Africa’s economy, help create jobs, and reduce reliance on imports, many of which fail to meet regulatory requirements. Ness says the SABS’s adoption of SANS IEC 62930 is a step toward stricter oversight, but until type 5 certification is available, it falls to installers and customers to verify compliance.
SOEW is a South African manufacturer of electrical cables, committed to advancing the nation’s renewable energy goals through high-quality, locally produced solutions.
For more information visit: https://soew.co.za/