Shutting down a whole process plant to attend to a single electrical problem means unnecessary downtime. The process plant at a gold mine in Ghana has become the first in Africa to install WEG’s fully withdrawable WEG CCM06 boards, which safely improve the plant’s flexibility by allowing for selected circuits to be isolated for maintenance and repair.

Foster Yeboah, Regional Sales Manager for West Africa and based at Zest WEG’s Ghana branch says, “The customer’s existing motor control centre regulated many operations, which all had to be shut down when a single item of equipment needed to be attended to. This led to significant downtime, which the customer wanted to avoid.
“The mine sought a solution which would allow for the electrical feed to specific equipment to be isolated, in turn allowing for targeted maintenance to be conducted on that equipment without necessitating a complete plant shutdown,” says Yeboah.
The answer came in the form of a double containerised electrical house or E-house with a key element of this solution being the fully withdrawable boards.
“The WEG CCM06 boards are compartmentalised functional units which can be turned off and pulled out, without affecting the power to the other units,” he explains. “This is a valuable feature when considering that important equipment such as mills and discharge pumps should ideally operate continuously to keep the plant efficient.”
With the new motor control centre (MCC), plant operators will be able to conduct a straightforward process of isolating the unit they want to check or repair – simply by opening a latch, turning a shaft and drawing out the relevant board. It is then secured to allow work to proceed safely on the equipment as needed, and the plant continues running. Yeboah emphasises that access to the live parts is not possible when the functional units are removed, significantly enhancing safety.
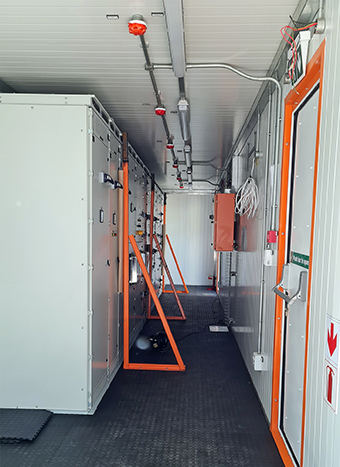
“Once a board is taken out, the design ensures that there is no risk of electrical shock to the operator,” he says. “To further enhance safety, the board can also be placed in ‘test’ mode for safe testing procedures.”
This means it can receive and display signals for testing while it is disconnected from mains power. The system also includes smart relays so operators can control the MCC remotely.
“In our experience, many process plants in our region operate under the same constraints as this customer, having to shut down completely when maintenance is carried out,” says Yeboah. “With this innovative, fully withdrawable board solution, we expect considerable interest from other operations.”
He highlights that a plant’s energy costs can also be significantly reduced by limiting the number of stoppages and restarts. With electric motors consuming a substantial portion of the energy in a process plant, continuous operation is an important factor in economising power consumption.
“Motors use much more energy on start-up so, by reducing the number of times they are stopped and started, plants can cut back on the peak starting current that pushes up energy costs,” he says.
The fully withdrawable boards are among a range of other WEG equipment that has been included in the E-house, which was constructed by Zest WEG at one of its South African manufacturing facilities.
A major advantage with E-houses is that all equipment can be installed and tested before shipping to site, and factory acceptance tests (FATs) can be conducted virtually to expedite customer sign-off.
Yeboah says Zest WEG’s Ghana office, with its team of competent sales engineers, has been running for more than 10 years. It also has a training centre for upskilling customers’ teams.
For more information visit: www.zestweg.com