Steve Hutchinson, marketing manager for South Africa’s inverter-based, microprocessor-driven welding machine manufacturer, Starweld, talks about the company’s new Trojan 600 engine-driven generator/welder/compressor combination, which has been locally designed to better meet the on-site needs of mining houses across Africa.
Click to download and read pdf
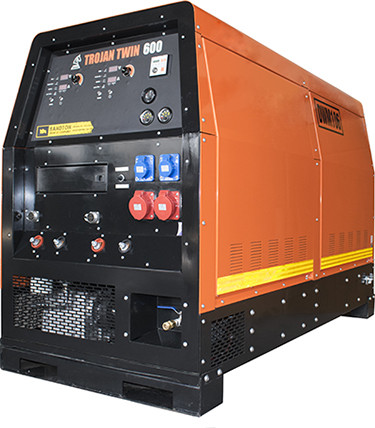
Robert Case and Steve Hutchinson first met 25 years ago when they were both involved in the manufacture and marketing of the South African-designed Modweld range of welding inverters. In 2011 they met up again, and founded Starweld, a company established to locally manufacture a high-end range of microprocessor-driven welding inverters. “We soon began to focus on the ‘yellow metal’ industry where welding equipment is used for manufacturing and refurbishing mining and earth moving equipment. This equipment has to be very durable, as it is typically used for heavy-duty MIG/MAG welding and arc air gouging,” Steve Hutchinson tells African Fusion.
The multi-process Orion 600 welding machine rapidly became the flagship machine of the Starweld range. It competes favourably with international brands dominating this market segment in South Africa. In its favour is that it goes to market at a significantly lower price than its international competitors, while spare parts such as the main PC board are readily available and at a much lower price.
A key advantage of the Orion 600 was brought to light when Sandton Plant, the largest hirer of yellow metal equipment to the country’s mining industry, appointed DG Power Services to conduct an independent survey to monitor the machine’s electrical usage: against the market leader’s heavier transformer-based machines. “The results were astounding. An overall saving of 40% was achieved when using the Orion 600. This resulted in Sandton Plant replacing all 15 of the company’s transformer based welding machines with Starweld Orion 600s,” notes Hutchinson, adding that these machines are used for heavy duty 1.2 mm MIG/MAG welding and arc-air gouging of earth moving buckets and tippers.
The Trojan 600 engine driven multipack
The findings from the Sandton Plant survey led Starweld to begin looking at adding an engine driven generator/welder/compressor combination to its range. “Once again this market was dominated by the same two international brands, and this made it difficult for newcomers to break in. The imported products, however, were sold at premium prices and spare parts were also expensive with lengthy delivery times,” says Hutchinson.
Starweld quickly learnt that, in Africa, there was a resistance to moving away from these tried and tested machines. For this reason they decided to design an engine-driven machine, utilising the internationally recognised Perkins engine range, where spare parts would be readily available across the continent.
Manufacturers of these engine driven welding machines have always opted for using ‘chopper technology’ and wired the welding units directly into the generator’s alternator. This enables them to get high welding current outputs, and it saves on space within the generator’s housing. The downside though is that the welding unit is part of the machine’s alternator and cannot be removed for servicing, or replacement.
Based on the fact that the inverter-driven Orion 600 had already shown itself to be economical on electrical usage, tests were conducted on running twin Orion 600s off a single Perkins 60 kVA genset. “Once again, the result beggared belief. It was found that two Starweld Orion 600s and a compressor can be run simultaneously. This was a world first,” suggests Hutchinson.
“In addition, if not wanting to arc air gouge while welding, a third MIG/MAG welder inverter could be plugged into the auxiliary power outlet, and all three units could then weld simultaneously. And, if the client wished to do only stick/MMA welding, two additional inverters could be plugged into the auxiliary power outlets, bringing the total number of stick welding operators using the same generator up to four,” he informs African Fusion.
The plug-and-play concept
The next challenge was to incorporate these findings into designing and building a generator/welder/compressor multipack. “The high performing Orion 600 is extremely compact; it only weighs 45 kg. So Starweld set about designing a modular ‘plug-and-play’ system, where removable faceless, welding units would be mounted on a shelf directly above the alternator. The welding controls and the digital displays were then placed on the front panel of the multipack, with plug-in connections to the power sources made via power cables and harnesses. “This became a further game changer, as a replacement power source could be installed with ease, and the operator could be welding again within an hour,” Hutchinson points out.
For arc air gouging, hydrovane-styled air compressors are used by both of the existing brands in the market. This saves on space and produces the large volumes of air needed for arc air gouging. However, the design has not proved to be robust in arduous African conditions and, unless serviced regularly and properly, expensive breakdowns result.
For an alternative option in its Trojan 600 multipack, Starweld decided to approach Warne’s Compressors, a company that has been involved in the local compressor market for over 70 years. A robust Italian piston-type Nu Air twin head compressor with a cast iron crank and high strength steel valve rods was selected. This was directly coupled to a 7.5 HP electric motor, and produced a continuous 30 cfm of compressed air. Warne’s further reduced the air reservoir down to 50 litres. Once again, the compressor, like the welding power sources, is powered off the alternator’s output, meaning that it can be easily removed for repairs.
Starweld’s engine driven Trojan 600 welding multipacks are now available in a number of different combinations, including:
- The Twin Air 600 with two Orion 600s, a compressor, two 380 V and two 220 V auxiliary outputs.
- The Single Air 600 with a compressor, two 380 V and two 220 V auxiliary outputs.
- And the generator with a Single Orion 600 without a compressor but with the two 380 V and two 220 V auxiliary outputs.
- Soon to be introduced is the Starweld Trojan 400 range, with a similar set of multipack options.
- Starweld’s Africa agent: Wolfram Mining Supplies
“Wolfram Mining Supplies, which was established in 1990, has been appointed to market our Starweld Range of welding equipment into Africa,” continues Hutchinson.
“Wolfram has a firm footprint across all the SADC countries. Core to the company’s mission is to ‘simplify technical support’ for its customers. Having previously been associated with several international welding brands, Wolfram understands the welding market, and has now chosen to partner with Starweld, and to exclusively market its products.
“The decision was based on the quality, performance and product support that Starweld provides,” Steve Hutchinson concludes.