Welding Specialist for Air Products in South Africa, Sean Young talks about shielding gas selection for optimised gas metal arc and gas tungsten arc welding (GMAW and GTAW), and the importance of understanding the role of each gas in the mix.
Click to download and read pdf
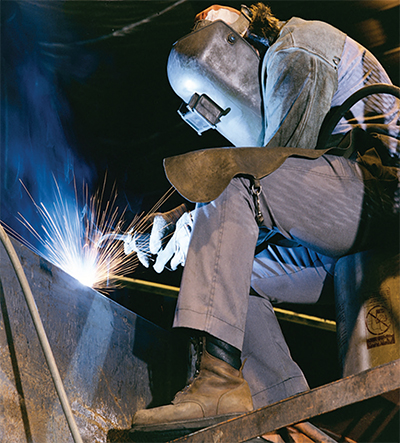
“Whether for manual or robotic welding, I have found that many welding gas customers do not understand how to match a shielding gas mixture to a GMAW or GTAW application to achieve the best results possible. They tend, instead, to stick to the same gas they first chose, the one they have always used and their distributor has always supplied. What they don’t realise is that the best choice for welding quality and productivity depends on the specific application, most importantly, the material being welded; the material thickness; and the welding process being used.
“There is always a specific gas mixture that will give the best result: better fusion, less spatter, better productivity and best possible welding stability,” begins Welding Specialist, Sean Young. “The selection of the specific gas mixture should be seen as an integral part optimising every welding procedure,” he says.
So how do we optimise the shielding gas choice? “I tend to get a good idea of what shielding gas will work by asking the customer three key questions: the process, the material being welded and the material thickness,” says Young.
If the process is GTAW, he continues, pure argon is the obvious shielding gas choice. “But is pure argon the best choice for all materials? For thin sheet and root welding of carbon and stainless steels, we would say yes, but what about copper and aluminium, which are excellent heat conductors that dissipate the heat of the arc very quickly? A significantly increased amount of heat is required and even on relatively thin section material, an argon helium gas mixture or even pure helium may provide far better results,” Young tells African Fusion.
Moving onto the semi-automatic GMAW welding process, he says argon gas remains the gas of choice for welding aluminium and copper and their alloys. “Again, though, helium in the gas mix is often advantageous, particularly when welding thicker section materials,” he notes.
For GMAW welding of steels, however, the gas choice becomes much wider, depending on the process variant – CV or pulsed – and is highly dependent on the material thickness.
“Mixtures of carbon dioxide and oxygen in argon are usually the obvious choices, but there are many and it is important to understand the role that CO2 and O2 play in the various mixtures,” he says.
In the GMAW welding arc, he explains, carbon dioxide disassociates into ions of carbon monoxide and oxygen in a reaction that releases heat. In the weld pool, this additional heat results in increased plate melting and deeper penetration, which can also result in faster welding speeds and better productivity.
“But on the negative side, raising CO2 levels leads to poorer arc stability, making it more difficult for the welder to manipulate and control the weld pool, which can result in incidences of lack of penetration and lack of sidewall fusion. Also, high CO2 levels in shielding gases are associated with spatter,” he says.
“For welding stainless steels, CO2 levels in the shielding gas should be limited to a maximum of 2% to prevent lamellar tearing: the carbon in the gas results in low ductility surface inclusions along the solidification front, which tear open on solidification due to internal stress,” Young points out.
On the role of oxygen, he says small percentages of O2 in a shielding gas mixture decrease the surface tension. “This accelerates the pinch effect, making droplet sizes smaller. It also results in a more fluid and flatter weld puddle,” he continues.
Smaller droplets also lead to smaller spatter particles being expelled from the weld pool, which often means they solidify in the air so they can simply be swept off the plate. This reduces the amount of post-weld grinding needed.
Carbon steel materials and plate thickness
Carbon steels are the most common materials welded with the GMAW process, and it is here that Young says there are the most opportunities for optimising the shielding gas choice. “Broadly speaking, you want a good compromise between weld stability, weld quality, penetration and speed,” he says.
For GMAW welding of thin section carbon steel plate in the 1.0 to 3.0 mm range, Young recommends a gas with a small percentage of O2 and low levels of CO2. “Coogar Plus is ideal. No additional heat is needed to penetrate the thin material and care needs to be taken not to burn through. This also applies to welding thin material onto thicker material. When a 3 mm section is being welded into a 20 mm section, a properly fused weld of 3 mm is required, there is no need to choose the gas to suit the thicker section material,” Young advises.
Magmix 3 delivers excellent arc stability, optimised metal transfer characteristics and good surface profiles for thinner materials. “It also offers a wider tolerance envelope with respect to the welding current, voltage and wire feed parameters, which means welders do not have to be 100% spot on with the machine set-up,” he adds.
For slightly thicker section carbon steel in the 3 to 8 mm range, Sean Young recommends the Magmix 3 shielding gas mixture, which has a little more CO2 to deliver deeper penetration.
“For high speed down hand position welding of steels in the 9 to 15 m range, we suggest Coogar 89, which is a mix that offers higher fluidity and heat. This, of course, makes the mix unsuitable for positional welding,” he advises.
Air Products’ Coogar 84, he says, has been developed for 12 to 20 mm carbon steel material, and Coogar 82 is recommended for a thick section plate of 20 mm and above. This mix does not contain oxygen because higher welding currents will typically be used, therefore increased fluidity is not needed.
“For robotic welding, particularly when using synergic or pulsed modes, we also recommend a two-part mix of argon and CO2 because, when pulsing, high stability is favoured over fluidity,” he says, adding that Air Products’ argon+CO2 Ultra Blend as well as the Coogar 82 mix are ideal for most spatter-free and automated pulsed GMAW applications.
“Welding optimisation is about making it as easy as possible for the welder to achieve the quality results required in the fastest possible time with the minimum amount of post weld cleaning,” notes Young.
“When welders struggle with stability and unwanted spatter while welding, the grinder must be removed after welding to clean the plate and joint. We look at what our customers are welding to optimise their process and to prevent them from having to pick up a grinder after every weld.
“By making shielding gas choices that are better matched with the specific material, selecting the correct material thickness and ensuring that the correct process is used, Air Products’ expertise can drastically assist in raising the weld quality and significantly raise productivity at the same time,” concludes Sean Young.