Bonfiglioli is a longstanding leading manufacturer of mechatronic solutions for the metalworking industry, providing excellence and innovation by staying focused on customers and their manufacturing needs.
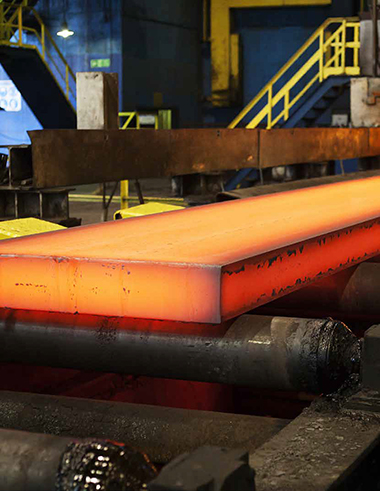
Thanks to know-how developed over many years and a long-term commitment to co-designing customised solutions with key players in the metalworking industry, Bonfiglioli can supply dedicated drive solutions from a wide product portfolio, along with integrating capabilities that combine both industrial and precision gearboxes with motors, servomotors, frequency inverters and controllers.
Today’s cutting, bending and punching machines are highly automated to achieve the precision and productivity required by sheet metal product manufacturers. A bending brake, for example, is typically under full electronic control, and might use six axes or more to position, accurately bend and then remove a part. Each requires a motor and a gearbox to drive its axes, and each motor will need to be controlled with respect to position and speed, typically by a frequency inverter such as Bonfiglioli’s Active Cube (ACU).
Each axis will have unique space, torque and power requirements, so many combinations of these three core components will be needed for any integrated mechatronic drive solutions for a metalworking machine. For the main bending axis drive of a press brake, a closed-loop Bonfiglioli ACU inverter can be used with a synchronous BMD reluctance motor to drive one of Bonfiglioli’s 300 series planetary gearboxes, for example.
For the crowning axis, however, which accurately controls the curvature of the bend itself, the ACU closed loop frequency inverter controls an F-Series parallel shaft gearmotor to deliver the perfect bend shape and finish.
Punching, shearing and bending functions can also be combined to form totally automatic and flexible production lines, with no intermediate handling. Bonfiglioli solutions can combine performance and cost effectiveness through the integration of best-fit mechatronic solutions for each of the many axes required for such systems. Drive options for the multiple axes for the whole machine might include: A-series servo right-angled gearmotors (BMD); LC-Series precision planetary gearboxes with BMD motors; and F-Series parallel shaft gearmotors with IE3 asynchronous motors, each with its own matching ACU frequency drive.
Laser tube cutting machines are another example. Now a common manufacturing process throughout the world, laser tube cutting is an advanced technique for cutting shapes and patterns –including holes, complex curves, and profiles – into 3D-formed tubes and formed structures or channels.
In terms of axes, these machines typically manipulate the workpiece rotation and positions underneath a laser cutting head, which is angled while operating to accommodate access and edge bevel requirements.
Laser tube metalworking machines can be fitted with a range of Bonfiglioli solutions, such as an open-loop inverter (AGL) controlling a VF/W worm gearmotor with an IE3 motor; or a closed-loop (ANG) inverter with a precision planetary-based servo gearmotor; or an open-loop inverter with a right-angled A-Series gearmotor. These are adaptable to existing machine designs and are easily incorporated, while saving space in control cabinets due to the high power densities of modern Bonfiglioli inverters.
On plate rolling machines Bonfiglioli solutions are used to help shape and form metal plate of different thicknesses. Gearmotors are used drive one or more pairs of rollers to obtain round or conical shapes through a calculated deformation process.
Bonfiglioli supplies a wide range of planetary hydraulic or electric gearmotors with controls to deliver the torque required for these processes at the highest levels of performance. The company’s 300 series planetary roller drives can be driven by hydraulic or electric motors. They have high overload capacity, good torque control and can accommodate shock loads up to 2 000 000 Nm. Associated ACU frequency inverters are available in the power range of 0.37 to 1 200 kW with a host of control and safety features. BX-Series asynchronous IE3 motors are generally preferred, and in terms of power, up to 355 kW can be accommodated.
Flanging machines for the manufacture of dished and flanged ends for tanks and pressure vessels are also accommodated. These machines require high performance to deliver maximum reliability and to achieve tolerance and lamination reduction requirements. Starting from circular plates of different thicknesses, flanging machines press/beat the plate repeatedly with specific tools to obtain a dished shape by cold forming. The final step in completing a dished end is to form the edge so that it is suitable for the circumferential seam weld that joins it to the cylindrical section.
Bonfiglioli mechatronics solutions for operating the flanging drive for forming these ends include the 300-Series planetary flanging drive or the HDP Series flanging drive, both of which can be coupled to a BX-Series asynchronous electric motors powered by an ACU.
Wire drawing is another metal working process. It reduces the cross section of the wire by pulling it through a series of dies. A type of forging process, drawing can be performed at hot, warm, or cold temperatures. Bonfiglioli offers purpose designed drum drives for this process, which can be based on its 300 Series planetary or parallel shaft HDP Series drum drives.
In addition, for cable extrusion and stranding, Bonfiglioli offers pulling capstan drives that can synchronise line and winding speeds. These are available using combined planetary/helical bevel gear units from the 3/H Series pulling capstan drive range. With nominal torque levels of up to 1 300 000 Nm, these offer extremely high transmissible torque and power, making them suitable for very heavy-duty applications. Here, speed control and power can be delivered by an Active Cube inverter and a BX HD Series motor.
In the heavy-duty metal forming industries, self-aligning roller beds are used for positioning and rotating large cylindrical structures in order to perform operations such as welding. The rotation of the structures is driven by ac-geared motors under variable speed control.
Bonfiglioli supplies a wide range of planetary, helical parallel and helical bevel gearmotors and controls that are ideal for these roller beds, providing the highest level of performances for different machine capacity in the most arduous conditions. The company has a range of self-roller drives, from the 300-Series planetary drive range, as well as from the A-Series helical bevel and F-Series parallel gearmotors, which can incorporate BX-Series IE3 motors powered by ACUs.
Hot metal processing is performed by different types of furnaces – reheating furnaces, heat treatment furnaces and furnaces for hot rolling mills – which produce billets, blooms, or slabs. These require motion and control solutions for hot roller table conveyors and for opening and closing furnace doors.
These applications require solutions designed for harsh temperature conditions. Bonfiglioli’s 300M-Series gives the flexibility to drive the input and output shafts of roller table conveyors. When coupled to an IE4 BSR synchronous reluctance motor, forced ventilation is not required at low operating speed, while accurate speed and torque control is possible when the motor is combined with an ACU drive – even in open loop operation.
Bonfiglioli hot metal solutions are the best in class in terms of meantime before failure and they suit the needs of continuous operations. In addition, reliability can be improved and unplanned downtime minimised thanks to condition monitoring solutions from the company’s IOT platform and sensors.
Hot metal roller drives are available for the roller tables, which are fundamental in steel production plants to transport the material to the different process stations. These rollers are commonly driven by electrical gearmotors, which can be directly connected to the roller shaft: one gearmotor for every roller; or one gearmotor driving a few rollers through gear and chain transmissions.
Output speed can be varied according to the process phase or to the material weight. Heavier material will have lower speed, so a wide range of motor speed options is fundamental. Bonfiglioli offers a wide product portfolio of optimised solutions for drives and controls with speed adjustment to match material handling and weight and specifications.
On the foundry side, ladle transfer cars with different shapes and capacities are used to transport molten metals. To handle the tipping function, two gearmotors are used controlled by a single ACU. The system can deliver smooth payload handling thanks to dedicated S-ramp and anti-sloshing functions embedded in the controller.
Many years of experience in developing mechatronic solutions for the metalworking industries has given Bonfiglioli the flexibility to combine its extensive range into machines with the tightest installation spaces. The company can provide optimised drive and control solutions for light, complex and heavy-duty metalworking applications, all with a view to improving performance, extending lifetimes, and saving on installation and operating costs.
Most notably, these and all Bonfiglioli’s mechatronic solutions for the metalworking industries are easy to retrofit onto existing machines that require upgrading, which is sure to improve durability and reduce maintenance requirements compared to traditional solutions.